Machines
Machine comparison KEH Series
- Robust machine design for the production of high-strength chains over a long period of time
- Continuous welding of all chain links in one cycle (link by link)
- Complete deburring of welding bead
- KEH 4.2, KEH 5.2 and KEH 7.2 have a greater output because of individually adjustable rpm numbers for welding, deburring and transport
- KEH 4.2, KEH 5.2 and KEH 7.2 have an upsetting system that is not connected with the control shaft
- The upsetting process can be freely programmed at the monitor
- There is no mechanical upsetting cam required
Please select wire diameter [mm]
KEH 3.2
from 3
to 6 mm
Wire diameter | 3 - 6 mm |
at max. 1,000 N/mm² | 3 - 5 mm |
at max. 900 N/mm² | 3 - 6 mm |
Inner link length (pitch) | 9 - 39 mm |
Output, chain links | 90 - 65 pcs./min |
Chain welding |
KEH 4.2
from 5
to 10 mm
Wire diameter | 5 - 10 mm |
at max. 900 N/mm² | 5 - 10 mm |
at max. 1,000 N/mm² | 5 - 9 mm |
Inner link length (pitch) | 13.5 - 50 mm |
Output, chain links | 75 - 50 pcs./min |
KEH 5.2
from 8
to 13 mm
Wire diameter | 8 - 13 mm |
at max. 900 N/mm² | 8 - 13 mm |
at max. 1,000 N/mm² | 8 - 12 mm |
Inner link length (pitch) | 21.5 - 65 mm |
Output, chain links | 55 - 34 pcs./min |
KEH 7.2
from 10
to 18 mm
Wire diameter | 10 - 18 mm |
at max. 1,000 N/mm² | 10 - 16 mm |
at max. 800 N/mm² | 10 - 18 mm |
Inner link length (pitch) | 27 - 100 mm |
Output, chain links | 45 - 18 pcs./min |
KEH 8
from 13
to 20 mm
Wire diameter | 13 - 20 mm |
at max. 750 N/mm² | 13 - 20 mm |
at max. 500 N/mm² | 13 - 20 mm |
Inner link length (pitch) | 32 - 130 mm |
Output, chain links | 27 - 14 pcs./min |
KEH 8
Chain welding machines for resistance butt welding round steel chains KEH series
Modern design with increased safety and operating convenience. Adjustment of operating ranges and tensile wire strengths to current market requirements, including stainless steel and adjusted to the chain bending machines KEB x.2 and KER x.2. Replacing the complicated mechanical system of control shafts with individual servodrives reduces tooling and set-up times because there is no mechanical set-up work required anymore and parameters can be saved for later use in the control system.
Consistent use of servo-technology in the new x.2 series
The threephase motor that continuously drove the control shafts has been replaced. All servoaxes movements are now made at a considerably reduced duty cycle. Upsetting system with integrated pre-stroke by two synchronously working servo-hydraulic axes. Chain is transported and rotated up/down via an electric servo-axis.
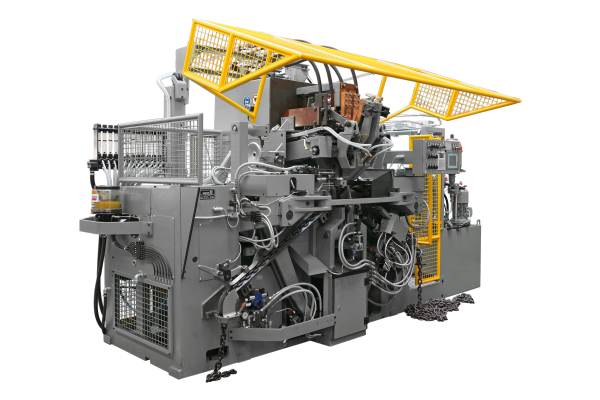