Innovative Technology for Hairpins, Axial Flux Coils and Busbars
E-mobility is on the rise and replaces the familiar combustion engine in many applications. The transformation to e-mobility requires machine manufacturers to develop solutions for sophisticated components.
WAFIOS offers unique machinery for the production of highly precise parts that are required in the production of powerful drives and current-carrying components.
Customized Solutions for your Production
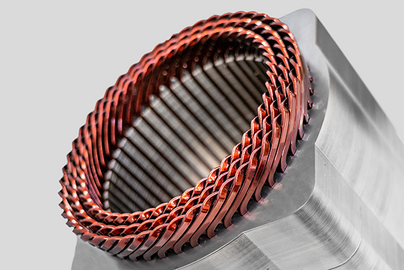
Sample Part Production
Based on the FMU E and BMF technology, we offer production tests and sample part productions of e-mobility components, from A samples for prototypes up to C samples for series machines, including prior theoretical feasibility tests of geometries.
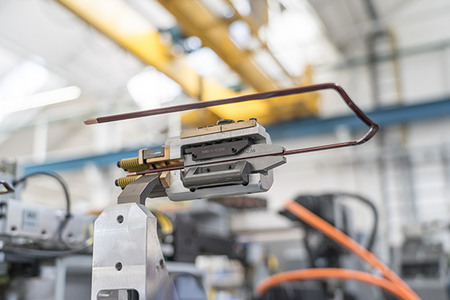
Hairpins
Over the past few years, hairpin stators have been widely used is automobiles. The FMU E is your machine for prototype and small-batch productions while our SpeedFormer, equipped with the latest HQ bending technology, meets your needs for large batches.
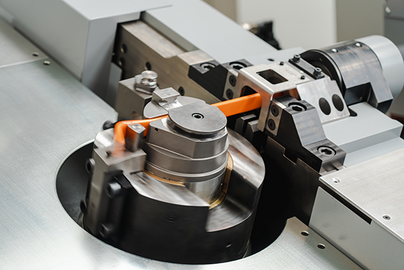
Busbars
The CNC technology of the BMF offers a completely new production concept for parts and busbars made of copper or aluminum flat wire (bare or insulated, PA 12, PEEK). It combines the process steps 'insulation stripping', 'bending' and 'cutting' in one machinery system.
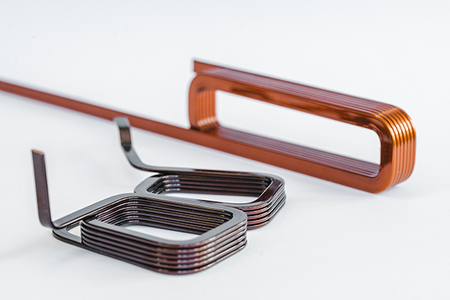
Axial Flux Coils
Edgewise bent coils are used for axial flux and radial flux motors with highest requirements and a lot of power. Our bending technology ensures minimum thickening and maximum use of the filling factor in the stator.
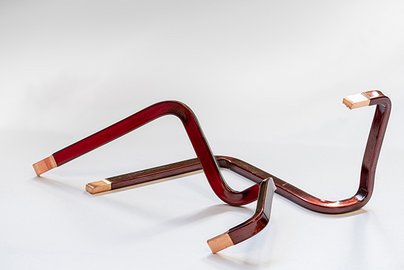
Stator Connection Assemblies
The stator is connected to the power electronics via an assembly composed of individual conductors. These conductors can be produced by bending or die cutting. As the installation space is limited, the geometry of these conductors is frequently very complex. A perfect job for the most flexible machine on the market!
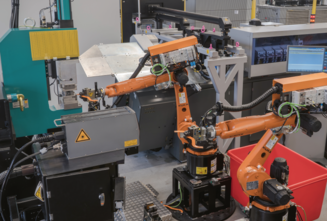
Automation Solutions
End-to-end automation solutions for e-mobility applications, like busbar bending machines of the BMF series. Automation solutions include punching, welding, feeding in and assembling stator connector parts, marking and other options. Improve your productivity and quality. Complete production system for stators in cooperation with the company Gehring.
HQ Bending Technique for Even More Precision
While hairpins produced with conventional bending techniques are subject to a little thickening at the bending point, the WAFIOS HQ bending technology (High-Quality Bending) ensures flat geometries. Special tools enable the production of the hair pin head without thickening. The s-shaped bend at the tip of the hairpin head can be produced without the formation of wings. Advantages are a flatter pin geometry and no thickening at the hairpin head which enables a smaller dimensioned stator basket. Highest precision with only one application.
Mechanical Milling Device for Busbars
Mechanical laser stripping or conventional laser stripping? Besides costs, also speed and amount of material removal are decisive factors for a suitable device. The mechanical milling device offers crucial advantages. With a cycle time of four to five seconds at a length of 40 mm material, the insulation stripping process can be carried out within the shortest period of time and is twice as fast as the laser insulation stripping process. The insulation can be stripped off either with round edges, notches or only at certain points. It can changed and adjusted via the WPS 3.2 EasyWay programming system at any time.
Our Accomplishments for your Inquiry:
Feasibility Study and Technical Advice
Tool Development and Production
Automation of Processes
Sample Part Production
FAQs - E-Mobility
WAFIOS offers comprehensive advice on all questions concerning your production system. In cooperation with Gehring Technologies GmbH + Co. KG we offer entire production systems for the production of hairpin stators. Enameled copper coils, as they are used in the automotive and electrical industries, can be produced with the FTU series. The BMF series offers highest precision in the production of busbars, even when producing smallest bending radii.
Our developments reflect state-of-the-art e-mobility technology and allow flexible bending processes for hairpins, busbars, copper coils as well as parts made of round and shaped wire.
3D bending is no problem due to the use of special tools. The new HQ bending technique combines in a unique way the advantages of forging tools with the flexibility of a CNC bending process. Compared to other technologies, this enables a highly flexible production and lower tool costs.
Laser and mechanical insulation stripping.
Batteries and motors are heavy components that increase the weight of vehicles. Lighter busbars made of aluminum and compact axial flux motors made of copper coils are a good possibility to reduce the weight of vehicles.
We offer to run in-house tests to find out which output is possible for your source material. Contact us.